Metal and technology sector, what are the risks?
Every day is different in the metal and technology sector and the diversity of activities is great. You have employees working in the workshop, but also on location with customers.
Employees maintain installations and are therefore also on the road a lot. These different workplaces all have their own specific risks.
We have listed a number of common risks in the metals and technology sector for you:
- Welding, cutting and drilling means there is a risk of cuts and burns.
- Due to bright light and noise, there is a risk of eye and hearing damage.
- We work with dangerous substances such as welding fumes, cleaning agents and/or oils.
- Due to machine work, there is a risk of accidents such as pinches or cuts.
- Because we work at height, there is a risk of falling.
Heavy equipment is often used in the metal and engineering sectors. As a result, employees have to deal with physical strain. Lifting and pushing materials and working in unpleasant positions will take its toll at some point.
The high workload, tight deadlines and the feeling of “always having to go on” put a mental strain on your employees. This is also something to include when preparing your risk assessment & evaluation.
Of course, we also looked at the current figures and facts. Unfortunately, we can conclude that the urgency for a good risk assessment & evaluation is great. The CBS figures show that in 2023, 2.5% of the technicians had an occupational accident involving absenteeism. That is almost double the national average (1.3%). The psychosocial burden is also rising in these sectors. This increase is mainly due to staff shortages and the high pressure to perform. The physical and mental risks are structurally present in the metal and technology sector.
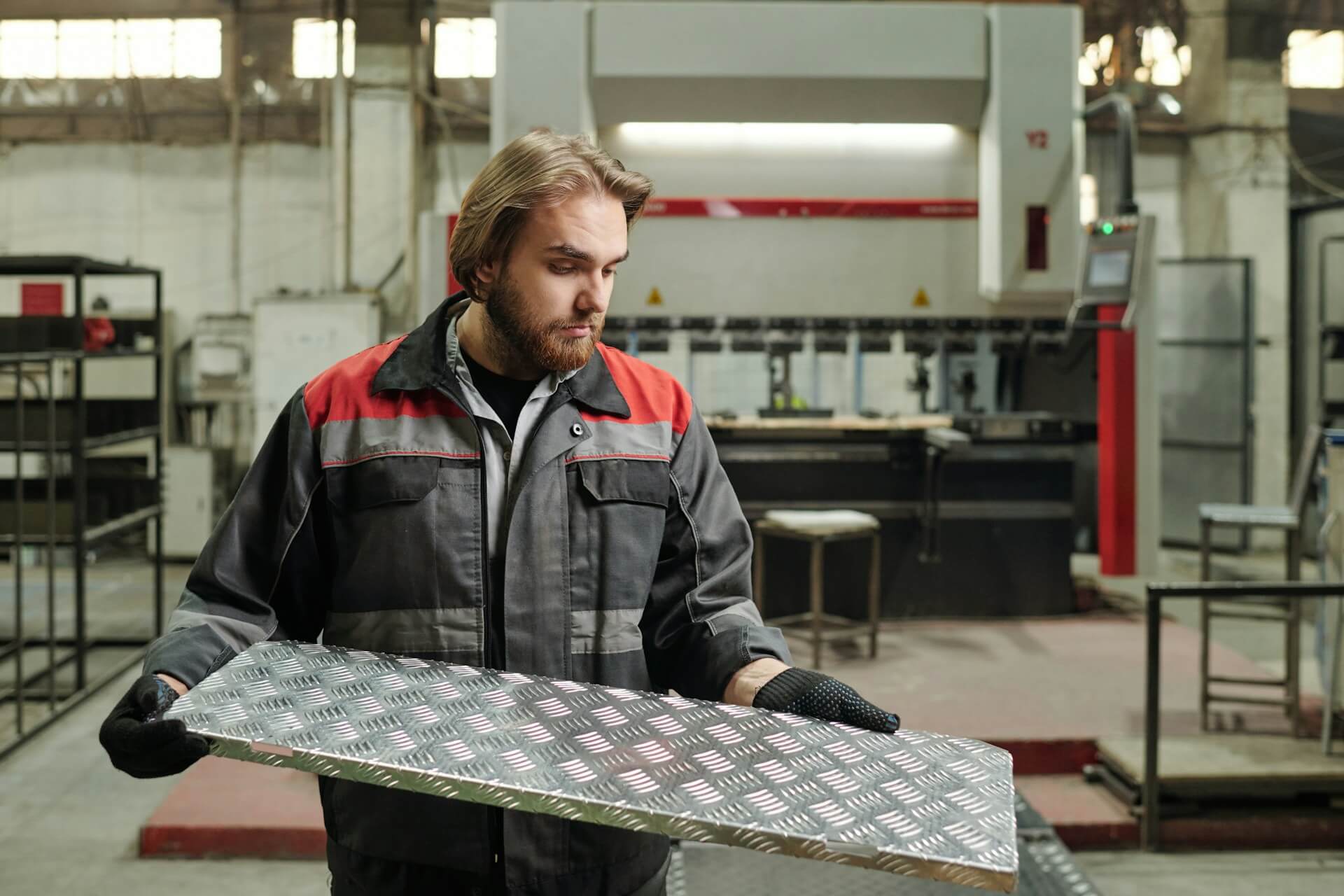
An risk assessment & evaluation, more than an obligation
Apart from the well-known “check mark” for the inspection, an risk assessment & evaluation provides guidance and guarantees the progress of your organization. An risk assessment & evaluation is much more than just that annoying legal obligation. What exactly can you do with a good and current risk assessment & evaluation? We list the benefits for you:
- You can organize processes in a safer and smarter way
- You can reduce absenteeism and prevent damage
- You can limit your costs
- You can keep employing employees for a longer period of time
With a good risk assessment & evaluation, you can work preventively. That is more pleasant than having to repair things afterwards. In sectors where deadlines are tight, heavy machinery is used a lot and even materials are heated, proactive work ethic and risk management are not a luxury. It is pure necessity.
An risk assessment & evaluation for metal and technology
The risks present in the metal and technology sector are different than in other sectors. In an risk assessment & evaluation for the metal and technology sector, only industry-specific risks are described. You won't find any standard lists in this risk assessment & evaluation.
The risks mentioned are really in line with your organization, with your employees and the existing work processes.
We would like to give you a few examples of existing risks per category.
Workplace risks:
- There are machines without a shield or an emergency stop.
- The maintenance of the equipment is poor and/or leaves much to be desired.
- There is too little or no ventilation when welding and/or cutting.
Personal risks:
- The PBMs are used incorrectly or not used at all.
- No certification or training is required to perform specialist work.
- Physical complaints occur due to an incorrect posture at work or the repetition of wrong movements.
Organizational risks:
- The work and time pressure are (too) high.
- Existing instructions and responsibilities are unclear
- There is no supervision of compliance with the procedures
The mental strain also plays a major role in the metal and technology sector. Unfortunately, this is still often forgotten in an risk assessment & evaluation while this risk certainly needs to be identified. When it comes to mental strain, think of stress, fatigue or the feeling of having to be “on” all the time.
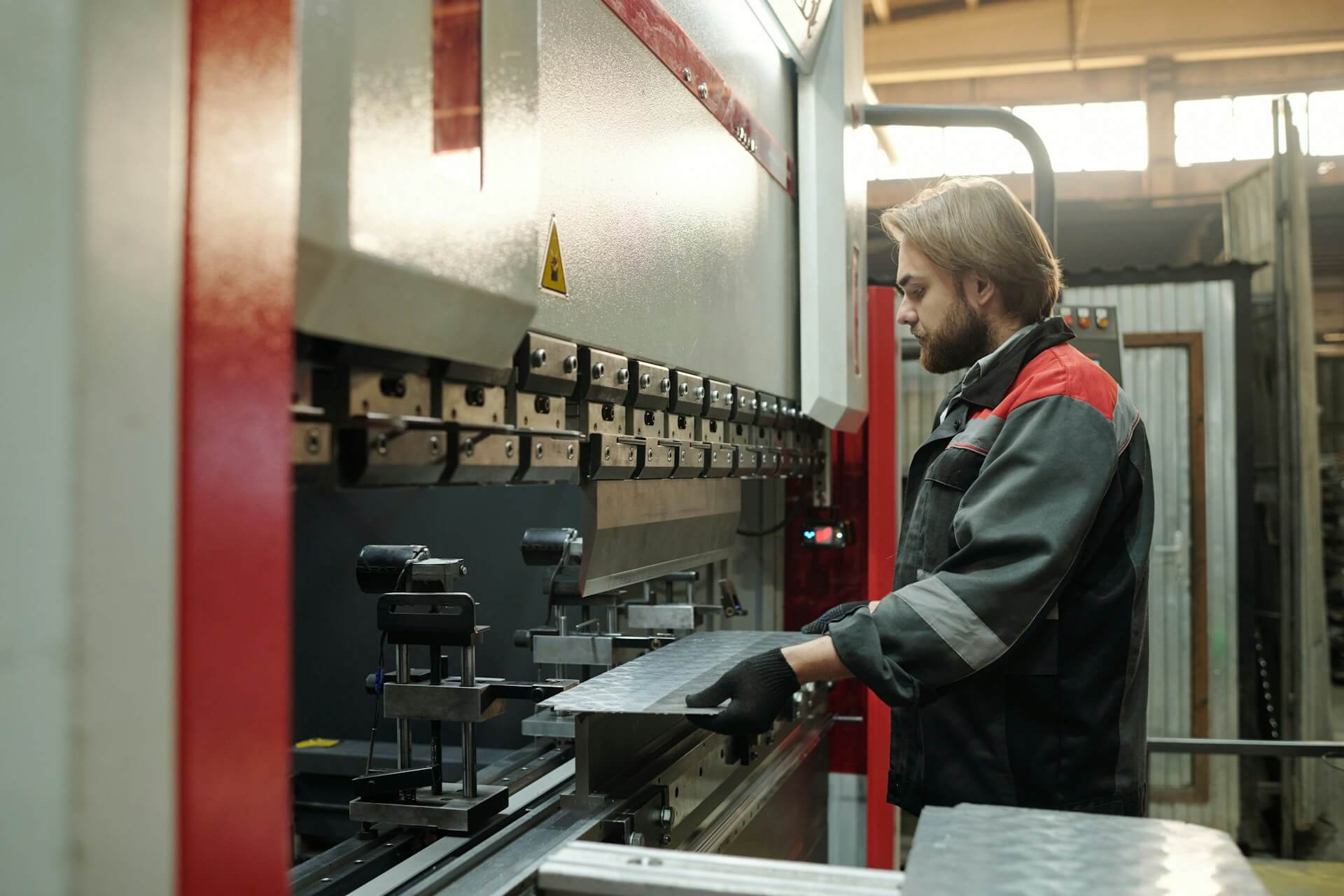
Setting up a good risk assessment & evaluation for technology companies in 6 steps.
Using the step-by-step plan below, we would like to tell you how you too can draw up a correct and up-to-date risk assessment & evaluation. Start by creating an overview. With the help of these steps, you will work in a structured and smart way:
1. Mapping functions and locations
Map out the functions within your organization. From welders to office workers, from mechanics to warehouse workers. You also include the workplaces and locations in your risk assessment & evaluation, not only the workplaces within your own building, but also customer work locations and maintenance sites.
2. Carrying out workplace inspections
Make sure you've seen all the workplaces with your own eyes. So you know exactly what's going on. View work processes, visit external work locations, and talk to your employees. Employees on the floor see other risks.
3. Identifying the risks
Each position has different risks. Clearly identify the risks per function. Your welder faces different risks than your warehouse employee. Work this out by function and by location.
4. Prioritizing risks
Use the risk matrix when prioritizing risks. What is the chance of something going wrong and what is the impact if it goes wrong?
5. Draw up an action plan
Determine the measures to be taken for each risk and make someone responsible. Set deadlines for which the measures must be implemented. Don't forget to include the follow-up of the measures in your plan of action.
Also read: How do you make an action plan for your risk assessment & evaluation?
6. Review your risk assessment & evaluation in case of changes
Have you purchased a new machine or have the work processes changed in the meantime? Don't forget to adjust this in your risk assessment & evaluation. Changes in your workforce must also be incorporated into the risk assessment & evaluation.
Common mistakes in an risk assessment & evaluation: here's how to prevent them!
When preparing a document, you always run the risk of making mistakes. Unfortunately, in the technology sector, we often see things go wrong when an risk assessment & evaluation is drawn up. We'll give you a few common pitfalls so you can prevent them:
- Only physical risks are mentioned, the mental strain is often forgotten.
- Processes are changing and new machines have been purchased, but this is not being modified in the risk assessment & evaluation. Every change requires an adjustment.
- Employees are not involved in drawing up the risk assessment & evaluation, so support is small and an incomplete picture of reality is created.
- The policy for PBMs is missing. There is no control over their use.
- The follow-up to the plan of action is missing. The measures have been noted and named, but they then disappear into the drawer.
Make sure you involve your employees in preparing your risk assessment & evaluation.
By also using a digital tool, you ensure that risks and measures are directly linked and monitored.
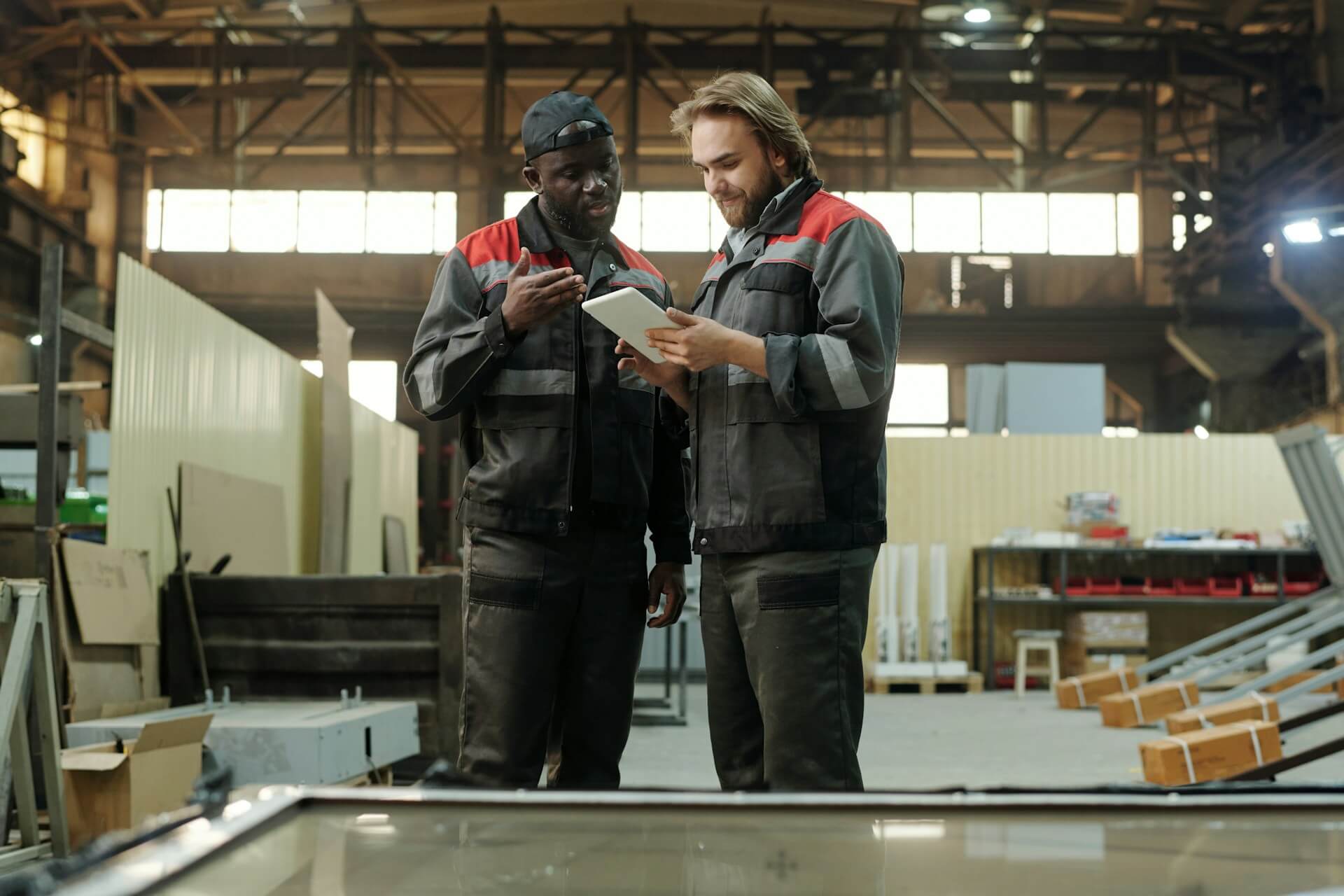
Tip: support and resources
For companies in the metal and technology sectors, an industry-specific risk assessment & evaluation is available. This can be found via the risk assessment & evaluation Support Center and has been approved by the SZW Inspectorate. The risk assessment & evaluation includes industry-specific risks and provides various exemplary measures.
Want more information? Have a look at CBS Occupational Accidents (current figures and trends) and on TNO Arbobalans Techniek, for scientific support and sector analyses.
Safety in technology, it starts with insight
Setting up an risk assessment & evaluation for the metal and technology sector becomes easier if you know what to look out for.
Want to know more about how ISO2HANDLE makes your risk assessment & evaluation easier? Check out our solution for the risk inventory and evaluation.
Quality, Health, Safety and Environment?